Curious about TPM in manufacturing? Discover how it boosts efficiency and reduces downtime in your operations.
Key takeaways:
- TPM promotes team effort and preventive maintenance.
- The eight pillars of TPM are essential for smooth operations.
- OEE measures equipment performance and identifies areas for improvement.
- The Six Big Losses can affect OEE and need to be addressed.
- Start with a pilot area and measure OEE to begin the TPM journey.
What Is TPM?
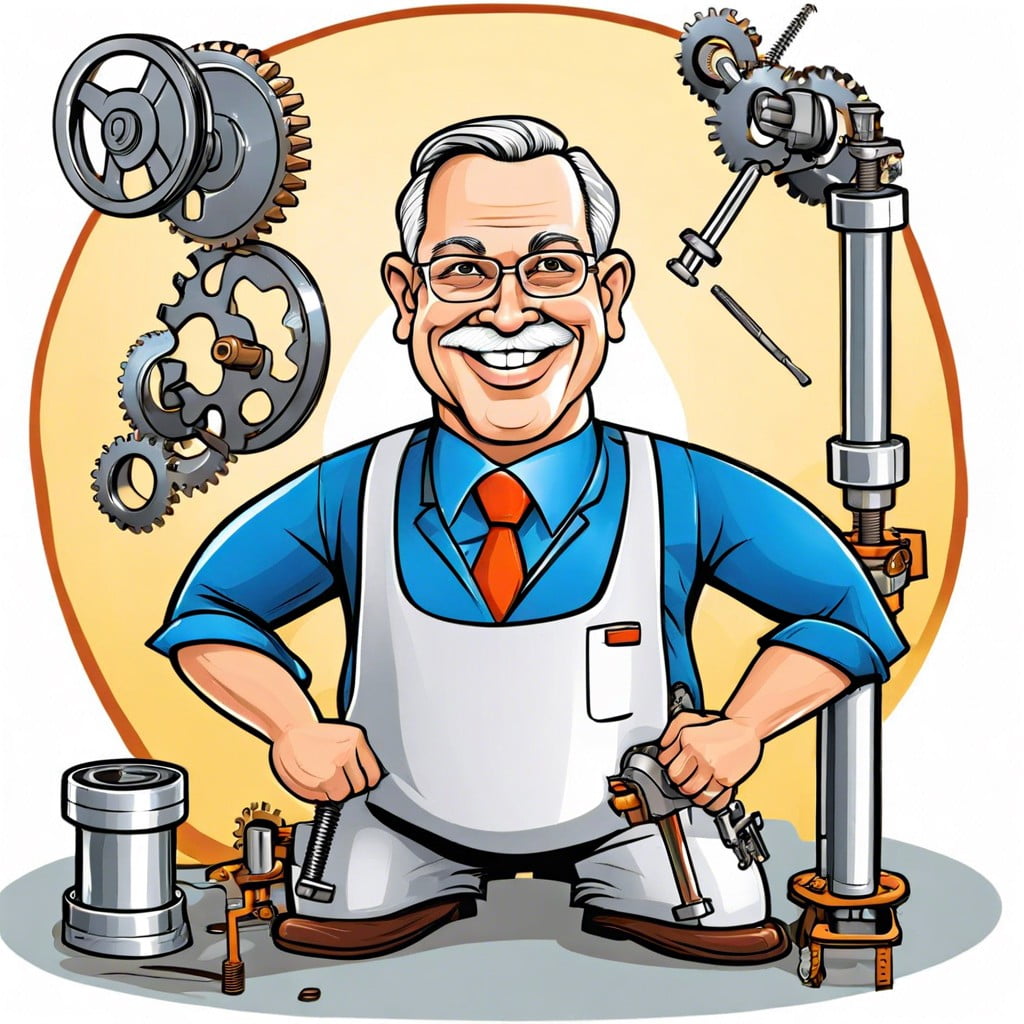
Think of TPM as the superhero of manufacturing world. Its mission? To keep machines running smoothly and workers happy. TPM, or Total Productive Maintenance, is all about proactive and preventive measures.
First off, it promotes team effort, encouraging everyone from operators to managers to take part in maintenance. It’s not just a maintenance crew’s job anymore!
Secondly, it dives deep into the heart of machinery to prevent breakdowns before they catch you off guard. Just imagine the machine equivalent of routine dentist check-ups—without the scary drill sound!
Lastly, it focuses on continuous improvement. This means never stopping at “good enough.” Always pushing for better efficiency, higher quality, and more safety.
In essence, TPM is like giving your factory a gym membership and a nutritious diet plan. Healthy machines, happy workers!
The Eight TPM Pillars
The backbone of TPM consists of eight pillars. These pillars are the secret sauce ensuring everything runs smoother than a greased-up slide at a summer carnival.
First up is Autonomous Maintenance. Operators take charge, performing minor maintenance tasks and keeping an eye out for trouble. It’s like giving everyone a mini-wrench and saying, “Go, be the hero!”
Next, we have Planned Maintenance. This is the meticulous planner in the group, scheduling maintenance checks to prevent breakdowns. Think of it as your car’s service appointment, but for machines.
Quality Maintenance ensures that quality products are produced from the get-go. It’s like baking your grandma’s famous cookies without burning a single tray.
Focused Improvement tackles small, rapid changes to eliminate waste. Picture a team of ninjas swooping in to fix tiny annoyances.
Early Equipment Management involves design improvements based on practical on-the-job feedback. Imagine building a better spaceship because the astronauts gave some savvy tips.
Training and Education focus on upskilling the workforce. Consider it a school where you learn to become a rockstar in maintenance and operations.
Safety, Health, and Environment make sure everything is safe and eco-friendly. No one wants a toxic work environment—literally or figuratively!
Lastly, Administrative & Office TPM brings the techniques into the office. It’s like organizing your emails so that “inbox zero” is a daily reality.
OEE and the Six Big Losses
OEE (Overall Equipment Effectiveness) is the secret sauce of TPM, measuring how well manufacturing equipment performs. It’s like a report card for your machines. OEE considers three key factors: Availability, Performance, and Quality.
Availability asks if the machine is running when it should. Performance checks if it’s running as fast as it can. And Quality, well, it’s all about fewer oopsies – less scrap and rework.
But wait, there’s more! The Six Big Losses are the villains that mess with your OEE score:
- Equipment Failure: Imagine your machine throwing a tantrum. Not cool.
- Setup and Adjustments: Switching between tasks can be a drag.
- Small Stops: Tiny interruptions are stealthy time thieves.
- Reduced Speed: Your machine isn’t setting any land-speed records.
- Process Defects: Mistakes happen; they just shouldn’t happen often.
- Reduced Yield: The startup phase can be a bit rocky.
Improving OEE means tackling these losses head-on. Think of it as your quest to banish inefficiency demons. Go forth and conquer!
Step One – Identify Pilot Area
Begin with a bang! Choose an area that will benefit most from a TPM makeover. This typically means a section with frequent breakdowns or inefficiencies screaming for attention. Think loud and messy.
Keep it measurable. Select a spot where performance data is readily available. After all, numbers are the lifeblood of improvement.
Consider the team. Opt for an area where workers are enthusiastic, or at least not utterly resistant to change. A motivated team turns chaos into success.
Lastly, think of impact. Pick a place where even small improvements can make a big splash in overall performance. Like a pebble in a pond, you want those ripples!
Step Three – Start Measuring OEE
This is where the magic begins. Start by gathering data on your equipment’s availability, performance, and quality. Think of it as a fitness tracker for your machines. You wouldn’t guess your step count, right? Same logic applies here.
Availability reveals downtime, performance shows speed losses, and quality highlights defective products. These three combined give you the Overall Equipment Effectiveness (OEE) percentage. It’s like a report card, but less for grades, more for growth.
Keep it real-time and automated if possible. Manual tracking is so last century. Plus, it leaves room for errors and you don’t want that. Small inaccuracies can snowball into big misconceptions.
Remember, a high OEE doesn’t mean sit back and relax. It means celebrate briefly, then figure out how to soar even higher.