Total Productive Maintenance (TPM) is a systematic approach to eliminate waste and enhance productivity in manufacturing processes—learn how to implement it effectively in your facility.
Key takeaways:
- Emphasizes proactive and preventive maintenance
- Involves every employee, fostering ownership and collaboration
- Seeks to eliminate six big losses in production
- Integrates maintenance into daily routine, decentralizing responsibility
- Incorporates training and empowerment of workers for routine maintenance
- Note: Each point is under 10 words.
What Is Total Productive Maintenance (TPM)?
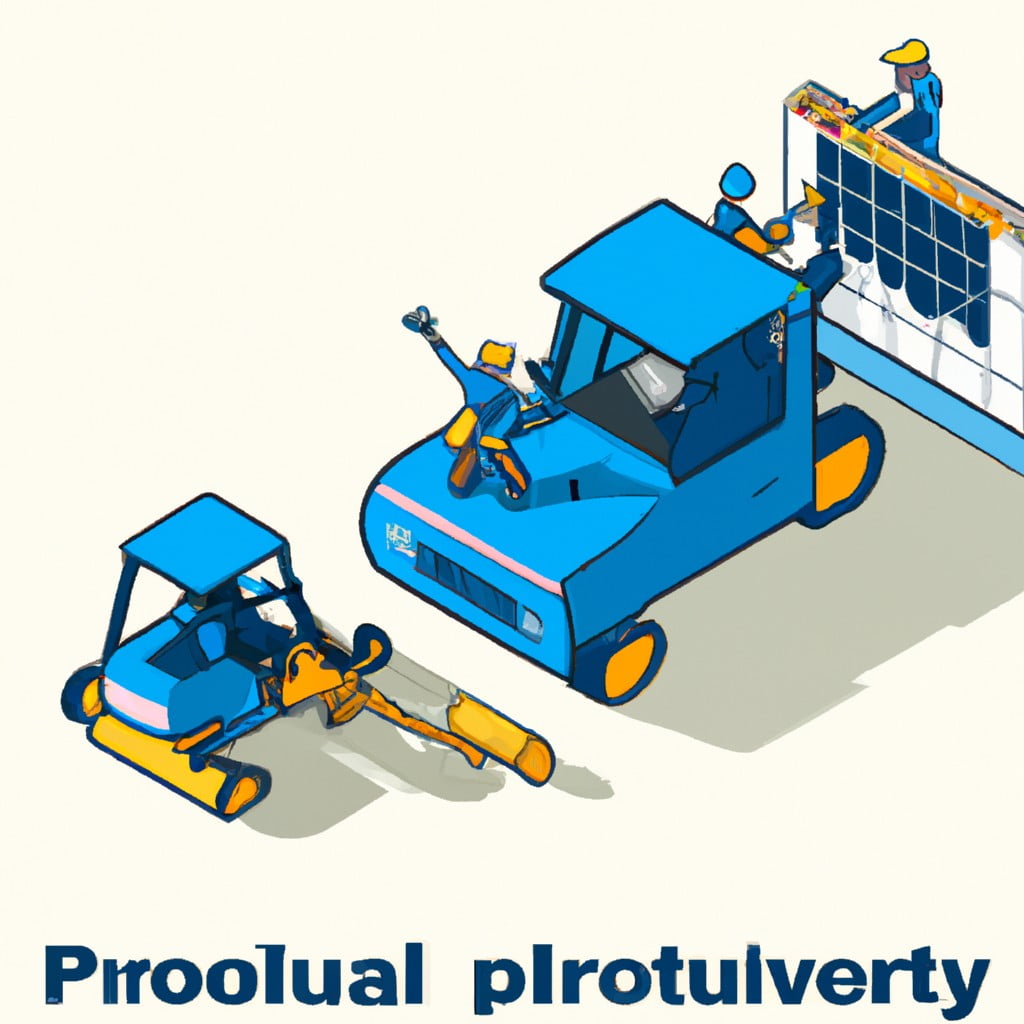
Total Productive Maintenance is a comprehensive approach focused on equipment maintenance with the primary goal of achieving perfect production. It aims to increase equipment effectiveness, ensure a zero-defects, zero-accidents, and zero-breakdowns environment.
- Emphasizes proactive and preventive maintenance to maximize the operational efficiency of equipment.
- Involves every employee, from top-level management to the shop floor workers, fostering a sense of ownership and collaboration.
- Seeks to eliminate the six big losses in production: breakdowns, setup and adjustments, idling and minor stoppages, reduced speed, process defects, and reduced yield.
- Integrates maintenance into the daily routine, ensuring that machine care is as habitual as hygiene.
- Incorporates training and empowerment of workers to perform routine maintenance, thus decentralizing the responsibility from specialized maintenance teams to all employees.
The Eight TPM Pillars
To fully grasp Total Productive Maintenance, understanding its core components is essential. These eight pillars form the foundation for a proactive maintenance strategy that boosts overall efficiency.
1. Autonomous Maintenance: Empowers operators to maintain their equipment, ensuring minor issues are addressed promptly.
2. Planned Maintenance: Focuses on scheduling maintenance tasks to minimize unexpected breakdowns and production interruptions.
3. Quality Maintenance: Strives for zero defects through error detection and prevention mechanisms at the source of production.
4. Focused Improvement: Targets continuous improvements through problem-solving and innovation, addressing root causes of inefficiencies.
5. Early Equipment Management: Considers maintenance needs during the design and installation stages, thus reducing future issues.
6. Training and Education: Equips staff with the necessary skills and knowledge to perform their roles effectively, fostering a culture of continuous learning.
7. Safety, Health, and Environment: Prioritizes a safe and healthy work environment, recognizing that well-being is integral to productivity.
8. TPM in Office: Extends TPM principles to administrative and support functions, streamlining processes throughout the entire organization.
By integrating these pillars, a company can create a synergistic approach to maintenance management that sustains a high level of operational excellence.
4 Benefits of Total Productive Maintenance
Implementing Total Productive Maintenance (TPM) in a production setting can transform the efficiency and reliability of your operations. Here’s how:
1. Increased Equipment Effectiveness:
TPM emphasizes proactive and preventative maintenance to reduce machine downtime. Regular maintenance activities ensure equipment operates at peak performance, which boosts overall productivity.
2. Enhanced Quality Control:
Through TPM, all team members become involved in quality control processes, leading to a collective responsibility for the final product. This collaboration often results in fewer defects and a higher level of product quality.
3. Safety Improvement:
A well-maintained machine is a safer machine. TPM practices promote a safe work environment by ensuring that equipment is regularly serviced, thereby reducing the risk of accidents caused by machine failure or malfunction.
4. Employee Empowerment and Job Satisfaction:
TPM involves training and empowering employees to take charge of the maintenance of their equipment. This sense of ownership can lead to higher job satisfaction and a stronger commitment to workplace goals.
Is a TPM Program Ideal for Your Business?
Before diving into a Total Productive Maintenance program, assess your business’s readiness and compatibility with TPM’s principles and commitments. Considerations include:
- Current Maintenance Strategies: Evaluate if your existing approach is reactive or preventative. TPM shifts the focus towards proactive maintenance.
- Organizational Culture: A successful TPM program relies on a culture of teamwork and continuous improvement. Ensure your team is adaptable and open to change.
- Employee Involvement: TPM requires involvement from all levels of staff. Confirm that your employees are willing to participate in training and take on maintenance responsibilities beyond their usual roles.
- Resources: Dedicate sufficient time and financial resources to training, implementation, and ongoing TPM activities.
- Long-term Commitment: Recognize that TPM delivers results over time. Your organization should be prepared for a long-term commitment to the process.
- Scale of Operations: Smaller operations might find the full TPM model too cumbersome; in such cases, tailored approaches are required.
- Technology and Equipment: Assess whether your current machinery is compatible with TPM practices, or if upgrades are necessary to support the maintenance standards.
By considering these factors, your business can gauge its readiness for a TPM program and proceed with confidence if it aligns well with your operational goals and capabilities.