Discover how implementing Total Productive Maintenance can significantly elevate your business operations by optimizing efficiency, reducing downtime, and increasing profitability.
Welcome to the world of Total Productive Maintenance (TPM), a comprehensive approach to improving business operations. In today’s fast-paced business environment, it is essential to optimize productivity and minimize downtime.
If you are looking for ways to enhance your business operations, TPM could be the answer you’re seeking. In this article, we will explore what TPM is, how it works, and the benefits it can bring to your organization.
So sit back, relax and get ready to learn about how TPM can elevate your business operations!
Defining Total Productive Maintenance
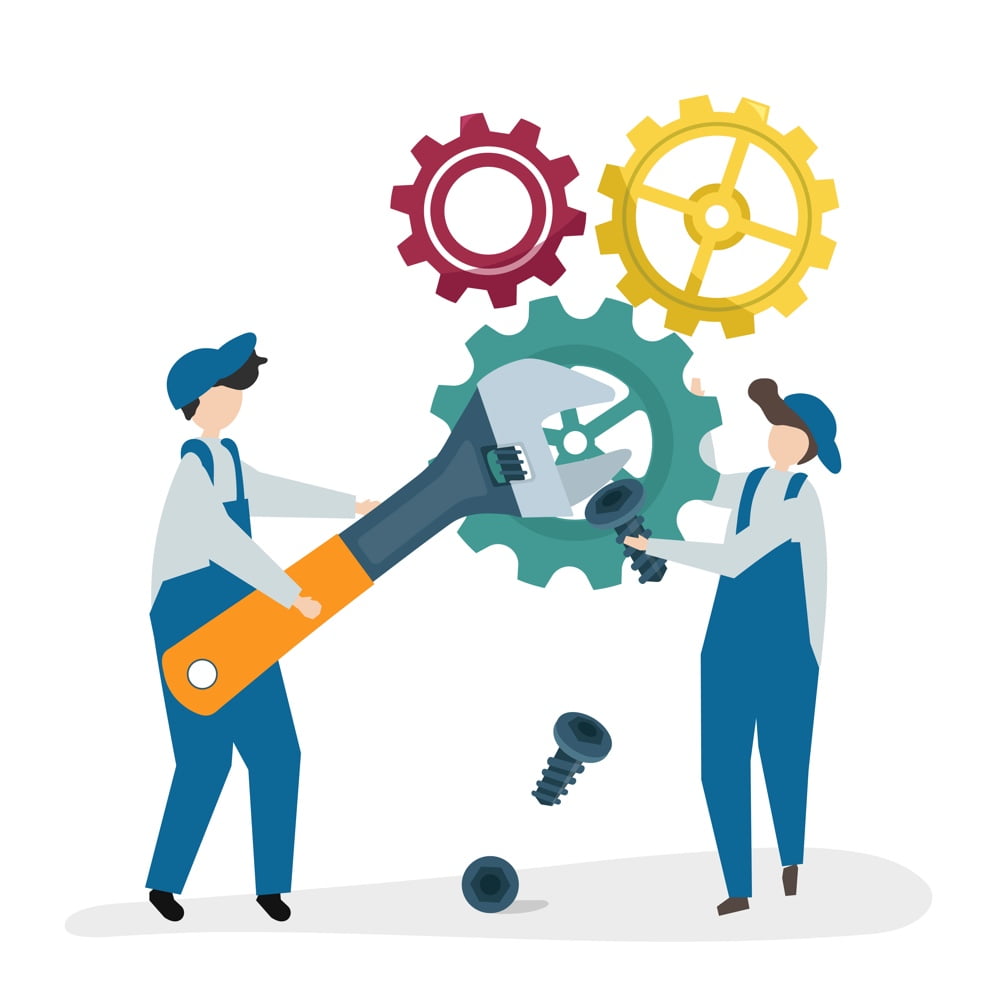
Total Productive Maintenance (TPM) is a comprehensive approach to equipment maintenance that aims to optimize productivity, reduce downtime, and increase profitability. It was developed in Japan in the 1970s as part of the Toyota Production System and has since been adopted by many companies worldwide.
TPM involves all employees at every level of an organization working together to improve equipment reliability, quality output, and safety.
At its core, TPM is about maximizing the efficiency of production processes while minimizing waste through continuous improvement efforts. This means ensuring that machines are always available when needed for production runs or other tasks without any unplanned downtime due to breakdowns or malfunctions.
In essence, Total Productive Maintenance seeks not only to maintain but also improve overall equipment effectiveness (OEE). OEE measures how well a machine performs relative to its maximum potential output under ideal conditions over time.
TPM Principles and Components
It aims to optimize equipment effectiveness, reduce downtime, and improve overall productivity by focusing on continuous improvement. TPM has eight pillars or principles that form its foundation:
1. Focused Improvement: This principle focuses on identifying opportunities for improvement in all aspects of the business.
2. Autonomous Maintenance: This principle empowers operators to take care of their equipment by performing routine maintenance tasks.
3. Planned Maintenance: This principle emphasizes scheduled maintenance activities based on data analysis and predictive techniques.
4. Quality Maintenance: The focus here is on preventing defects from occurring rather than detecting them after they happen.
- S Foundation
- : The 5S methodology provides a structured approach for organizing workspaces, reducing waste, and improving efficiency.
- Improving Overall Equipment Effectiveness (OEE): OEE measures how effectively an asset can produce quality products at maximum speed with minimum downtime.
- The Six Big Losses : These are six areas where businesses typically experience losses – breakdowns, setup time loss, reduced speed loss,
- quality defect losses,
- start-up yield losses,
- and minor stoppages
- Skills Development : TPM requires employees at all levels to have specific skills related to their roles so they can contribute effectively towards achieving organizational goals.
The Eight Pillars of TPM
These pillars provide a framework for improving equipment reliability, reducing downtime, and increasing productivity. The eight pillars include:
1. Focused Improvement: This pillar focuses on identifying and eliminating losses in production processes.
2. Autonomous Maintenance: This pillar empowers operators to take responsibility for maintaining their equipment.
3. Planned Maintenance: This pillar involves scheduling maintenance activities based on data-driven insights to prevent breakdowns.
4. Quality Management: This pillar ensures that quality is built into every process from start to finish.
5.Skills Development :This Pillar emphasizes training employees with the necessary skills required to operate machinery effectively.
6.Early Equipment Management :This Pillar aims at ensuring that new machines are introduced without any hitches or problems.
7.Environmental Health & Safety (EHS): EHS is an essential aspect of TPM as it ensures safety measures are put in place while carrying out maintenance operations.
8.Office TPM – Office-based activities such as administration can also benefit from applying TPM principles by streamlining workflows and optimizing efficiency.
Implementing these eight pillars requires commitment, resources, and a willingness to change existing practices within your organization’s culture gradually.
The 5S Foundation of TPM
The five S’s stand for Sort, Set in Order, Shine, Standardize and Sustain. These principles are designed to create an organized and efficient workplace by eliminating waste and improving productivity.
Sort involves removing unnecessary items from the workspace to reduce clutter and improve safety. Set in Order focuses on organizing tools, equipment, materials or information so they can be easily accessed when needed.
Shine refers to cleaning up the work area regularly to maintain cleanliness standards while also identifying potential problems such as leaks or damage that could lead to downtime if not addressed promptly.
Standardize aims at creating consistent processes across all areas of operation through standard operating procedures (SOPs) which help eliminate variations leading to inefficiencies.
Finally comes sustain which ensures continuous improvement by making sure everyone follows established procedures consistently over time while also encouraging feedback from employees on how things can be improved further.
Improving Overall Equipment Effectiveness
OEE measures the efficiency and effectiveness of equipment by analyzing three key factors: availability, performance, and quality. By improving these factors, businesses can increase productivity while reducing downtime.
Availability refers to the amount of time that equipment is available for use during scheduled production hours. Downtime due to breakdowns or maintenance reduces availability and negatively impacts OEE.
Performance measures how well equipment performs its intended function during production runs compared to its maximum potential output rate.
Quality reflects how often products meet customer specifications without defects or rework requirements. Poor quality results in wasted resources and lost revenue.
The Six Big Losses in TPM
These losses are referred to as the Six Big Losses, which include equipment breakdowns, setup and adjustment time, idling or minor stoppages, reduced speed or rate loss, defects and rework loss, and startup yield loss. By identifying these six big losses in your business operations through TPM analysis techniques such as Overall Equipment Effectiveness (OEE), you can take steps towards reducing them.
Equipment breakdowns occur when machines fail unexpectedly due to wear-and-tear or other issues. Setup time refers to the amount of time it takes for a machine operator to prepare a machine for use after it has been idle.
Idling occurs when machines are not being used but still consume energy while minor stoppages refer to short interruptions that halt production temporarily.
Reduced speed happens when machinery operates at less than its maximum capacity while defects result from poor quality control measures leading up-to final product inspection stages resulting in rework costs. Start-up yield refers specifically only during start-up periods where there may be initial waste before reaching optimal performance levels.
Autonomous Maintenance and Its Benefits
It involves empowering operators to take responsibility for the maintenance and upkeep of their equipment, reducing reliance on dedicated maintenance teams. By implementing AM, businesses can reduce downtime caused by minor stoppages and defects while improving overall equipment effectiveness.
The benefits of AM are numerous. First, it helps create a culture of ownership among operators who become more invested in the performance and longevity of their machines.
This sense of ownership leads to increased pride in workmanship and better communication between departments.
Secondly, AM reduces unplanned downtime by identifying potential issues before they escalate into major problems that require extensive repairs or replacements.
Autonomous maintenance frees up time for dedicated maintenance teams to focus on more complex tasks such as predictive or preventive maintenance strategies that further improve machine reliability over time.
Planned Maintenance Strategies
This involves scheduling regular maintenance activities to prevent equipment breakdowns and reduce downtime. Planned maintenance strategies can be divided into two categories: time-based and condition-based.
Time-based strategies involve performing routine inspections, lubrication, cleaning, and other preventive measures at predetermined intervals. These intervals are based on manufacturer recommendations or historical data analysis.
Condition-based strategies rely on monitoring equipment performance through sensors or other diagnostic tools to detect signs of wear or potential failure before they occur. This approach allows for more targeted maintenance interventions that can extend the life of your equipment while minimizing downtime.
Implementing a combination of both time- and condition-based approaches can help you achieve optimal results in terms of reducing unplanned downtime while maximizing productivity levels. Planned maintenance is an essential component in Total Productive Maintenance that helps businesses optimize their operations by preventing unexpected downtimes caused by machine failures.
Quality Maintenance Techniques
It focuses on ensuring that equipment and processes are operating at optimal levels to produce high-quality products consistently. Quality maintenance techniques involve identifying potential defects, analyzing root causes, and implementing corrective actions to prevent recurrence.
One of the most effective quality maintenance techniques is the use of Statistical Process Control (SPC). SPC involves monitoring a process over time using statistical methods to identify any variations or abnormalities in performance.
By doing so, it helps operators detect problems early before they become major issues that can lead to downtime or product defects.
Another technique used in quality maintenance is Failure Mode and Effects Analysis (FMEA), which identifies potential failure modes for each piece of equipment or process step. This analysis allows teams to prioritize their efforts based on risk level and develop preventive measures accordingly.
Overall Equipment Effectiveness (OEE) measurement also plays a crucial role in quality maintenance by providing insight into how well machines are performing relative to their maximum capacity. OEE considers three factors: availability, performance efficiency, and product quality rate; this information enables businesses’ decision-makers with data-driven insights into where improvements need implementation within production lines.
Focused Improvement in TPM
It involves identifying and eliminating losses in the production process to improve overall efficiency. The goal of Focused Improvement is to continuously identify areas for improvement, prioritize them based on their impact on productivity, and implement solutions that will eliminate or reduce those losses.
To achieve this objective, TPM teams use various tools such as Root Cause Analysis (RCA), Pareto Charts, Fishbone Diagrams, and Statistical Process Control (SPC) charts. These tools help identify the root causes of problems so that corrective actions can be taken.
The Focused Improvement pillar also emphasizes employee involvement in problem-solving activities. By involving employees at all levels in identifying issues and implementing solutions through cross-functional teams or Kaizen events helps create a culture of continuous improvement within an organization.
By focusing on improving processes rather than just fixing equipment breakdowns when they occur leads to significant improvements in productivity over time. This approach not only reduces downtime but also improves product quality while reducing costs associated with waste materials or rework.
Focused improvement plays a crucial role in achieving TPM’s goals by helping organizations optimize their operations continually.
Skills Development for TPM Success
It is essential to have the right skills and knowledge within your team to ensure successful implementation. The success of TPM depends on the ability of employees at all levels, from operators to managers, to understand its principles and apply them effectively.
Training programs are an integral part of developing these skills. They should cover not only technical aspects but also soft skills such as communication, problem-solving, teamwork, leadership development that are necessary for effective collaboration across departments.
Investing in employee training can lead not only lead towards better productivity but also increased job satisfaction among employees who feel valued by their employer’s investment in their professional growth.
Skills development is crucial for implementing Total Productive Maintenance successfully.
TPM and Safety Management
By implementing TPM principles, you can identify potential hazards early on and take proactive measures to prevent accidents from occurring. For example, autonomous maintenance tasks such as cleaning equipment or replacing worn-out parts not only improve machine reliability but also reduce the risk of injury to operators.
Moreover, TPM encourages employees at all levels to participate actively in safety management by promoting open communication channels for reporting unsafe conditions or incidents promptly. This approach fosters a culture of continuous improvement that prioritizes employee well-being while optimizing productivity.
Integrating safety management into your overall TPM strategy can help minimize risks associated with equipment failure or human error while improving operational efficiency.
Measuring TPM Results and Metrics
Measuring TPM results and metrics helps you understand how well your organization is performing, identify areas for improvement, and make data-driven decisions.
There are several key performance indicators (KPIs) that businesses can use to measure their TPM success. These include Overall Equipment Effectiveness (OEE), Mean Time Between Failures (MTBF), Mean Time To Repair (MTTR), Planned Maintenance Percentage Compliance, Autonomous Maintenance Completion Rate, Quality Defect Rate Reductions, Energy Consumption Reductions among others.
By tracking these KPIs over time using a reliable system or software toolset designed for this purpose will help you determine if your business operations are improving as expected or not. It also enables you to pinpoint specific areas where improvements need to be made so that corrective actions can be taken promptly.
Measuring the results of Total Productive Maintenance implementation provides valuable insights into how well it’s working in practice.
Implementing TPM in Your Business
Implementing TPM can be challenging, but with proper planning and execution, the benefits are well worth the effort.
The first step in implementing TPM is to create a plan that outlines your goals and objectives. This plan should include timelines for implementation as well as specific tasks that need to be completed along the way.
Once you have a plan in place, it’s time to start training your employees on TPM principles and techniques. It’s essential to get everyone on board with this new approach so they can understand their role in making it successful.
Another critical aspect of implementing TPM is identifying areas where improvements can be made. This could involve analyzing data from equipment downtime or conducting audits of work processes.
It’s also important to establish metrics for measuring progress towards achieving your goals. These metrics will help you track performance over time so you can make adjustments if necessary.
Ongoing review and adjustment are crucial components of successful implementation. Regularly reviewing progress against established metrics will allow you to identify areas where further improvement may be needed or adjust strategies based on changing circumstances within your organization or industry trends.
Overcoming TPM Implementation Challenges
TPM requires a significant shift in mindset and culture, which can be difficult to achieve. However, with proper planning and execution, you can overcome these challenges.
One of the most common challenges is resistance to change from employees who may not understand or believe in TPM’s principles. To overcome this challenge, it is essential to communicate clearly about what TPM entails and how it will benefit everyone involved.
Another challenge is identifying areas that need improvement within your organization accurately. It would help if you had accurate data on equipment performance metrics such as Overall Equipment Effectiveness (OEE), downtime analysis reports before implementing any changes.
A lack of resources such as time or budget constraints could also hinder successful implementation of TPM practices. In this case, prioritizing critical areas for improvement based on their impact on business operations could help allocate resources more effectively.
Finally yet importantly; sustaining momentum after initial success might prove challenging without continuous monitoring and review processes in place.
Ongoing TPM Review and Adjustments
Ongoing TPM review ensures that the program remains effective and relevant to your organization’s needs. It also helps identify areas for improvement and opportunities for further optimization.
During ongoing TPM reviews, you should evaluate how well each of the eight pillars of TPM is functioning within your organization. You can use metrics such as Overall Equipment Effectiveness (OEE) or Mean Time Between Failures (MTBF) to measure performance against established benchmarks.
Adjustments may be necessary if certain aspects of the program are not delivering expected results or if new challenges arise in operations. For example, changes in production volume or equipment upgrades may require modifications to planned maintenance schedules.
Regular communication with employees involved in implementing and maintaining TPM is crucial during ongoing reviews. Their feedback can provide valuable insights into what works well and where improvements could be made.
Ongoing review and adjustments are critical components of a successful Total Productive Maintenance program implementation.
Choosing the Right TPM Tools and Software
Choosing the right tools is essential for ensuring that your TPM implementation is successful. There are many different types of TPM software available, including computerized maintenance management systems (CMMS), enterprise asset management (EAM) solutions, and overall equipment effectiveness (OEE) tracking software.
When selecting a tool or system for your business, it’s important to consider factors such as ease-of-use, scalability, integration with existing systems, cost-effectiveness and vendor support. It’s also crucial to involve key stakeholders in the selection process so that everyone has input into which solution will work best for their needs.
By choosing the right TPM tools and software you can streamline processes across departments while improving communication between teams. This leads to better decision-making based on real-time data insights from all areas of operations – ultimately resulting in increased productivity levels throughout your organization.
The Role of IoT and Industry 4.0 in TPM
This technological revolution is also transforming Total Productive Maintenance (TPM), enabling businesses to monitor equipment performance in real-time, predict maintenance needs, and optimize production processes.
By integrating IoT sensors into their machinery, businesses can collect data on machine performance metrics such as temperature, vibration levels or energy consumption. This data can then be analyzed using advanced analytics tools to identify patterns that indicate potential issues before they occur.
In addition to predictive maintenance capabilities offered by IoT devices, Industry 4.0 technologies like artificial intelligence (AI) and machine learning algorithms can help improve overall equipment effectiveness by optimizing production schedules based on demand forecasts or identifying opportunities for process improvements.
As TPM continues to evolve alongside these emerging technologies it will become increasingly important for businesses looking to stay competitive in today’s fast-paced business environment.
Integrating TPM With Lean Manufacturing
While TPM focuses on optimizing equipment performance, reducing downtime, and improving overall efficiency, Lean Manufacturing aims to eliminate waste in all forms of production processes.
The integration of these two approaches can lead to a more streamlined operation that maximizes productivity while minimizing costs. By combining the principles of TPM with those of lean manufacturing, businesses can achieve greater levels of operational excellence.
One way to integrate these methodologies is by using the 5S foundation as a starting point for both approaches. The 5S methodology involves sorting out unnecessary items from workspaces (Seiri), setting things in order (Seiton), cleaning up work areas (Seiso), standardizing procedures (Seiketsu) and sustaining improvements over time(Shitsuke).
This approach helps create an organized workplace where everything has its place and is easily accessible when needed.
Another way to integrate TPM with lean manufacturing is through continuous improvement initiatives such as Kaizen events or Value Stream Mapping exercises. These activities help identify opportunities for improvement across all aspects of production processes including maintenance practices.
Future Trends and Development in TPM
In recent years, there has been a growing trend towards integrating TPM with Industry 4.0 technologies such as the Internet of Things (IoT) and Artificial Intelligence (AI). By leveraging these advanced technologies, businesses can gain real-time insights into their equipment performance and identify potential issues before they occur.
Another emerging trend in TPM is the integration of Lean Manufacturing principles. This approach emphasizes continuous improvement through waste reduction and process optimization.
By combining Lean Manufacturing with TPM practices, businesses can achieve even greater levels of efficiency and productivity.
Looking ahead to the future development in this field, we expect that more companies will adopt a proactive approach to maintenance by implementing predictive maintenance strategies powered by machine learning algorithms that analyze data from sensors embedded within machinery components.
Total Productive Maintenance continues to be an essential tool for optimizing business operations across various industries worldwide.
FAQ
Why is total productive maintenance important in business organization?
Total productive maintenance is important in business organizations because it maximizes performance, ensuring a higher quality of products, faster delivery, reduced errors, and fewer customer complaints.
What is total productive maintenance and why is it important?
Total Productive Maintenance (TPM) is a maintenance program that aims to improve productivity by keeping equipment consistently available and preventing unscheduled downtime.
What is the effectiveness of total productive maintenance?
The effectiveness of total productive maintenance (TPM) lies in its ability to empower workers to identify and manage potential risks, leading to improved equipment efficiency and the prevention of issues before they occur.
What is total productive maintenance for operational excellence?
Total Productive Maintenance (TPM) is a holistic approach that aims to maintain and improve the quality, production, and safety by fostering a strong relationship between workers and machinery in pursuit of operational excellence.
How does Total Productive Maintenance contribute to reducing equipment downtime in businesses?
Total Productive Maintenance contributes to reducing equipment downtime in businesses by implementing proactive maintenance practices that improve equipment reliability and efficiency.
What are the key elements and steps to implement Total Productive Maintenance in an organization?
Key elements and steps to implement Total Productive Maintenance include setting goals, establishing a cross-functional team, providing necessary training, implementing preventive maintenance, improving equipment efficiency, and continuously evaluating performance.
How can a comprehensive Total Productive Maintenance program lead to continuous improvement in business operations?
A comprehensive Total Productive Maintenance program can lead to continuous improvement in business operations by systematically maximizing equipment efficiency, reducing downtime, and fostering a proactive maintenance culture.