Setting the material ledger productive for the valuation area ensures accurate and transparent financial tracking of inventory and material costs across your business.
Key takeaways:
- Setting the material ledger productive ensures accurate financial tracking.
- Material ledger is important for informed decisions, legal compliance, and profitability analysis.
- Steps to set material ledger productive: check system settings, activate relevant valuation areas, define material ledger types, ensure data accuracy, and run regular performance checks.
- Common pitfalls: inadequate initial setup, incorrect data entry, neglecting system updates, and overlooking user training.
- Best practices: update and cleanse data consistently, encourage cross-departmental collaboration, train staff on system updates, leverage system features, and perform periodic audits.
Importance of Material Ledger for Valuation
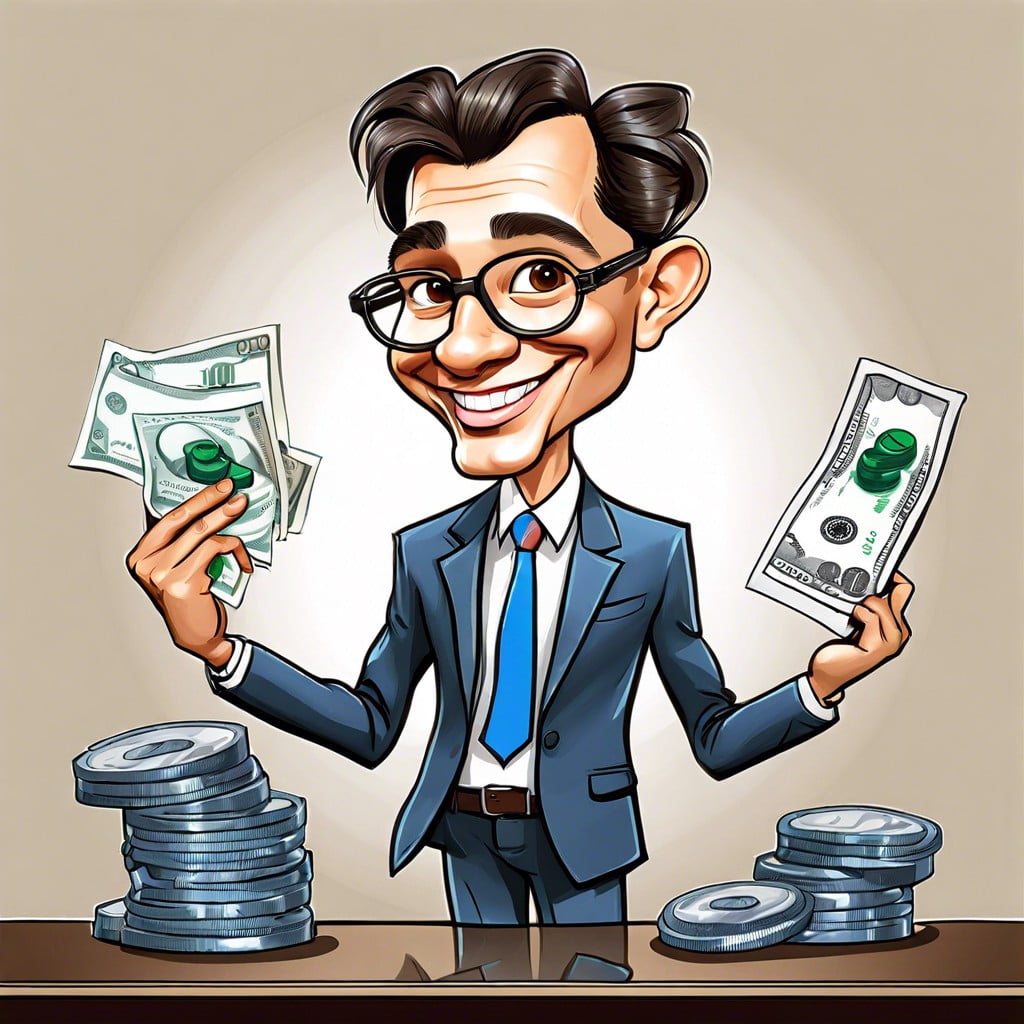
Think of the material ledger as your company’s financial GPS. It guides you through the labyrinth of materials and costs, helping you trace every dollar and every dime. When you’re navigating valuation, it’s crucial.
First off, accurate cost tracking helps in making informed business decisions. You wouldn’t drive blindfolded, right?
Second, legal compliance. Nobody likes a run-in with the tax folks. Maintaining a material ledger that’s set up correctly ensures you’re sticking to the rules.
Third, profitability analysis. Knowing what things cost helps you price them right. It’s like knowing the secret cookie recipe but for your finances.
Lastly, coherence across departments. Everyone from procurement to sales speaks the same financial language. No more “lost in translation” moments. In short, the material ledger keeps the ship sailing smoothly and everyone on the same page – or ledger.
Steps to Set Material Ledger Productive
Alright, let’s get your material ledger humming like a well-oiled machine. First, ensure your system settings in the ERP are spot on. You don’t want any gremlins in your configuration.
Check that all relevant valuation areas are active. This is crucial. Nobody wants to do all this work in a dead zone.
Next, make sure you’ve properly defined the material ledger types. Think of them like superheroes with different powers, ready to swoop in and save your valuation day.
Data accuracy is your friend. Your enemy? Inaccurate beginning balances and inconsistent postings. Audit those numbers like you’re Sherlock Holmes with a magnifying glass.
Finally, run regular performance checks. A productive material ledger isn’t a “set it and forget it” entity. It’s more like a pet that needs regular feeding and the occasional trip to the vet.
Who knew numbers could be this exciting, right?
Typical Pitfalls and How to Avoid Them
Ah, pitfalls, the uninvited guests at every implementation party! When setting up a material ledger for valuation, a few common traps can sneak up on you. Avoid them, and you’re halfway to gold.
First, inadequate initial setup. Missing the necessary configuration parameters can lead to a world of pain. Double-check your settings before moving forward. Think of it like assembling IKEA furniture: miss a screw, and everything wobbles.
Second, incorrect data entry. This might sound obvious, but even a tiny error can snowball into a major problem. Make sure the data fed into the system is accurate and thoroughly vetted. It’s like feeding your dog chocolate—not advisable!
Third, neglecting to update the system regularly. Business environments change, and your settings should too. Schedule regular audits to keep everything up-to-date. It’s like giving your car a tune-up; neglect it and expect a breakdown.
Last but not least, overlooking user training. An amazing tool is worthless if no one knows how to use it. Invest in training programs for your team. After all, even a wizard with no spell book is just a robed human.
So, sidestep these landmines to ensure smooth sailing!
Best Practices
Ensure proper data management by consistently updating and cleansing data. This avoids inaccuracies that create financial headaches.
Encourage cross-departmental collaboration, because who doesn’t love a good team effort? Finance, logistics, and production should all be on the same page.
Regularly train your staff on system updates and best practices. No one wants to be the person still using dial-up in a fiber-optic world.
Leverage system features such as automated reporting to save time and reduce human error. Think of it as having a reliable assistant who doesn’t take snack breaks.
Perform periodic audits to catch any discrepancies early. It’s like checking your teeth for spinach before a big meeting.
Establish clear processes for cost allocation and inventory valuation. Consistency is key; it’s the reliable friend who’s always there when you need them.