Learn how to create an engaging and effective Total Productive Maintenance PowerPoint presentation to keep your audience invested.
Key takeaways:
- Preventive Maintenance: Maintaining equipment before issues arise.
- Autonomous Maintenance: Operators taking responsibility for basic upkeep.
- Planned Maintenance: Scheduled check-ups to avoid breakdowns.
- Quality Maintenance: Ensuring equipment operates without defects.
- Objectives of TPM: Boost efficiency, reduce downtime, promote safety, involve employees.
- Benefits of TPM: Increased productivity, safer workplace, cost savings, improved quality.
- Steps to Implement TPM: Assess, set goals, involve everyone, train staff, pilot projects, measure and analyze, keep improving.
- Equipment Effectiveness: Availability, performance, and quality determine effectiveness. Downtime is the enemy.
Definition of Total Productive Maintenance (TPM)
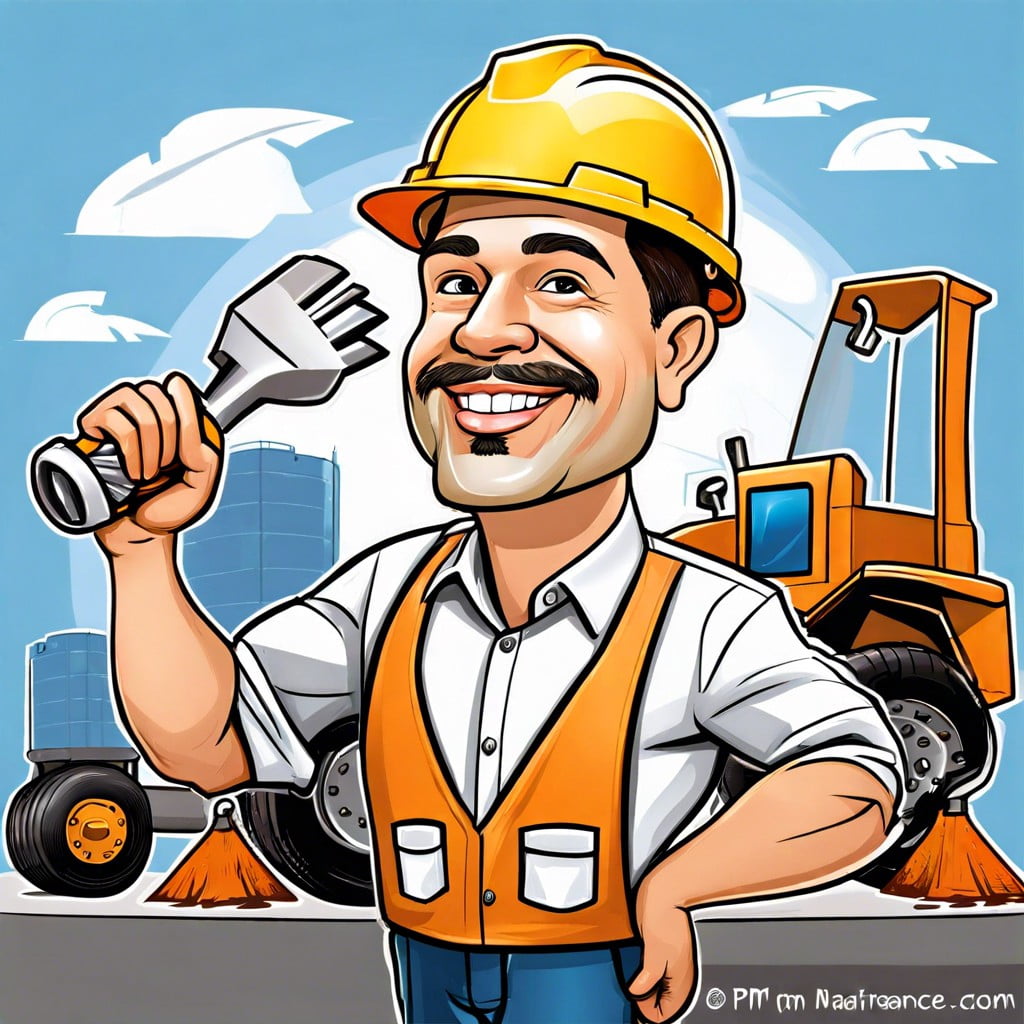
Originating from the land of cherry blossoms and sushi masters (Japan, for the uninitiated), TPM is all about keeping your machines and equipment happier than a kid in a candy store. It aims to improve productivity by involving everyone—yes, even Jerry from accounting—in maintenance activities.
Picture it as a health plan for your machinery, ensuring optimal performance while minimizing downtime. It’s proactive, preventive, and very pragmatic.
- Here are some key concepts:
- Preventive Maintenance: Think of it like brushing your teeth before cavities show up.
- Autonomous Maintenance: Empower your operators to take charge of basic upkeep, no more babysitting.
- Planned Maintenance: Scheduled check-ups to avoid the dreaded “crash and burn” scenarios.
- Quality Maintenance: Ensuring equipment operates without hiccups, because nobody likes surprise parties with defects.
And voilà, the magic of TPM.
Key Objectives of TPM
Enhancing equipment efficiency sounds like a snooze fest, but it’s like giving your machines a daily dose of espresso! TPM aims to boost the overall effectiveness of equipment, ensuring that they perform at their peak potential.
Reducing downtime is another key goal. Think about it: sick days for machines? Not a great idea. TPM works to minimize those unexpected breakdowns that have everyone running around like headless chickens.
Safety and maintenance are not just buzzwords here. TPM emphasizes creating a safer working environment, because nothing kills productivity like a workplace catastrophe.
Employee involvement is crucial. Imagine the team high-fives when everyone from the janitor to the CEO is invested in keeping operations running smoothly. TPM fosters this sense of shared responsibility and collaboration. This isn’t just about keeping things moving; it’s about making everyone feel like a superstar contributor.
Benefits of Implementing TPM
Boosting productivity, anyone? With Total Productive Maintenance by your side, you’ll certainly get there. One major perk is sky-high equipment effectiveness. Imagine your machines running like a Swiss watch—less downtime, fewer hiccups, and more products flying out the door.
Feeling that workplace zen? TPM creates a safer, happier environment for everyone. Less chaos and fewer breakdowns mean fewer injuries. Bonus: happy workers are productive workers.
Cost savings will have your finance team doing cartwheels. Effective TPM slashes repair costs and extends the lifespan of equipment. It’s like finding money under the couch cushions, but better.
Say goodbye to surprise breakdowns. TPM’s regular maintenance schedules help you nip potential problems in the bud. It’s the equivalent of eating your veggies every day—small efforts that lead to big health rewards.
Lastly, let’s talk about quality. You’ll see fewer defects and a smoother production process. Your end products are pristine, and your customers? Pretty darn pleased.
Steps to Implement TPM
First things first, assess the current state of your equipment. It’s like checking if your car has enough fuel before a long trip.
Next, set clear TPM goals. Aim high but keep it realistic. Dream big, but you don’t want anyone trying to turn water into wine here.
Then, involve everyone. Yes, everyone. From the janitor to the CEO. It’s like a team-building exercise, but with less falling into each other’s arms and more fixing machinery.
After that, train your staff. Make sure they know what they’re doing. An untrained team is like an army of monkeys with wrenches.
Launch small, pilot projects. Think of these as the training wheels. Test the waters before diving in.
Measure and analyze the results. Use those numbers. They’re friends, not foes. If spreadsheets were superheroes, they’d be Captain Accountability.
Lastly, keep improving. It’s a marathon, not a sprint. Adjust, refine, and keep it rolling. Run like it’s a never-ending treadmill but with fewer watch-your-step signs.
Isn’t that much better than a 1,000-page manual?
Equipment Effectiveness and Downtime
Let’s dive into the nitty-gritty of keeping your machines humming! Think of equipment effectiveness as the report card for your machinery. A+ means they’re working their magic flawlessly, while any grade lower means more work (and headaches) for you.
Three key factors determine effectiveness: Availability, Performance, and Quality. Availability checks if the equipment is up and running when it should be. No sneaky naps allowed! Performance looks at speed and efficiency, because who has time for a slowpoke? Quality ensures the output isn’t just fast, but also primo stuff. No one wants a shiny new paperweight.
Downtime? That’s the villain here. It’s like your machine decided to take a coffee break. Unplanned downtime means stress, lost productivity, and increased costs. Planned downtime, however, is a hero in disguise, allowing for maintenance and preventing bigger issues. Manageable, right? Now, let’s keep those machines in tip-top shape and banish downtime with the power of TPM.